Online condition monitoring on Boliden mine hoist
Mining
작성자
spmkorea
작성일
2023-09-19 15:58
조회
95
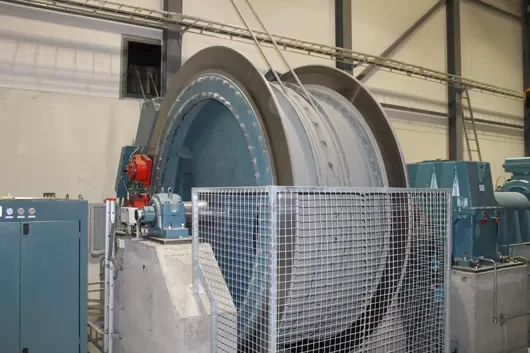
Online condition monitoring on Boliden mine hoist
At the Renström mine in northern Sweden, Boliden monitors the mechanical condition of the multi-rope friction hoist using a combination of vibration and high definition shock pulse measurement.
The hoist is a process critical application used in underground mines to either transport ore to the surface or personnel to or from the mine shaft. This case study describes a friction hoist application in the Renström mine; currently Sweden’s deepest mine at 1340 m. The ore is polymetallic and contains zinc, copper, lead, gold and silver, which is extracted using the cut-and-fill method.The hoist was installed in July 2013, at which time the condition measurements also started, providing good baseline measurements on a brand-new hoist. The hoist basically consists of a frequency-controlled motor, a two-stage gearbox, a drum, the wires and two skips. The skips are mounted at the tail end of the wires with a lifting capacity of approximately 5 tons each.
Early on, vibration measurements on the input shaft of the gearbox clearly indicated a mismatch between the gearbox data provided by the supplier and actual measuring results. It was later confirmed that the supplier had provided an incorrect gearbox drawing. Signs of outer race damage and possible unbalance have also been detected in the first six months of measurement.
The combination of vibration and shock pulse technologies is optimal for this type of application. Shock pulse transducers pick up bearing related signals very clearly, yielding crisp and easily interpreted readings, while vibration transducers pick up gear mesh frequencies in the gearbox, unbalance in the drum and other low frequency vibrations.