SPM LR/HR
Bearing Monitoring
작성자
spmkorea
작성일
2023-09-25 16:47
조회
507
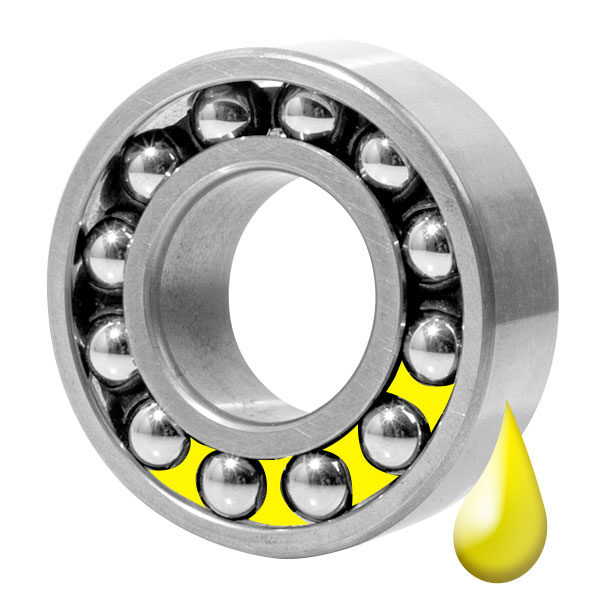
SPM LR/HR
회전하는 계면에서 정밀한 유막 상태 분석이 가능하며 최상의 윤활제를 선정 할 수 있습니다. 윤활 불량은 베어링 손상의 가장 큰 원인입니다.
Technical description
Measuring LR/HR
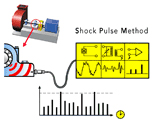
베어링에서 발생하는 쇼크 펄스는 매질을 통하여 전파되며 이를 SPM transducer가 취득, 전기 신호로 변환하여 쇼크 바닥 값, 쇼크 피크 값을 표시합니다.
쇼크 펄스 측정 장비는 2가지 진폭 레벨이 결정 될 때까지 측정 임계값을 변화시키면서 발생 빈도(초당 발생하는 쇼크 펄스)를 계산합니다.
HR, 쇼크 펄스 하이 레이트(대략 초당 100회 발생하는 쇼크의 바닥 값)
LR, 쇼크 펄스 로우 레이트(대략 초당 40회 발생하는 강한 쇼크의 값)
LR, HR은 원시 값(raw value)로 dBsv(decibel shock value) 값 입니다.
LR/HR Input data
SPM LR/HR 기술에서는 베어링 크기, 사이즈는 물론 베어링의 형태가 HR 측정값에 영향을 주기 때문에 보다 정교한 데이터 입력이 필요합니다. 그래야 손상 되지 않은 베어링의 윤활 상태도 분석 할 수 있습니다. RPM, 베어링 사이즈에 베어링 타입이 추가 됩니다. 최상의 방법은 Condmaster Ruby의 베어링 카탈로그에서 ISO 베어링 넘버를 검색하여 입력하는 것이며 가장 정확합니다.
LR/HR Evaluation
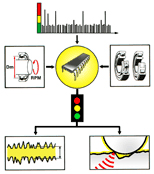
LUB 넘버: 유막 상태 값
COND 넘버: 표면 손상 값LUB 넘버가 0이라는 것은 드라이 러닝하고 있음을 의미하며 유막 두께에 따라 증가합니다.
COND 넘버가 30 정도라는 것은 표면의 스트레스 혹은 손상 초기임을 의미하며 손상이 심해짐에 따라 증가합니다.CODE A, 베어링 상태 양호
CODE B, 윤활 불량
CODE C, 베어링 드라이 러닝, 손상 위험
CODE D, 베어링 손상
SPM Condmaster Ruby에서 LR/HR과 관련한 LUBMASTER는 Shock pulse 데이터, 윤활제 종류, 점도, 사용 온도를 계산하여 지금의 조건에서의 베어링의 잔여 수명을 계산합니다. 윤활제의 타입, 점도 변경이 잔여 수명에 미치는 효과도 계산 할 수 있습니다.
LR/HR Calibration
베어링의 로드가 최소로 걸리거나 적절한 측정 포인트에서 측정이 힘든 경우(표준 이하의 신호 강도), SPM LR/HR 기술의 정확도는 보정 팩터(COMP 넘버)를 사용하여 보완합니다. 베어링 카달로그, 윤활제의 특성 데이터를 기반으로 SPM의 LEONOVA(INTELLINOVA)은 양호한 상태의 베어링의 일반적인 쇼크 레벨을 계산하고 비정상적으로 적은 신호에 이를 보정하여 결과를 평가합니다.
LR/HR 스펙트럼 분석(SPM Spectrum)
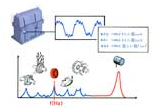
거의 모든 베어링의 주파수 패턴들은 Condmaster Ruby에 이미 내장되어 있습니다. Condmaster Ruby의 심프텀 그룹에서 ‘베어링’을 링크하면 사용자는 해당 베어링 이름을 클릭하여 베어링 패턴을 간단하게 조명할 수 있습니다. 또한 Gear mesh 패턴과 같은 다른 심프텀도 확인 할 수 있습니다. 스펙트럼에서 베어링 스펙트럼이 선명하게 일치한다는 것은 측정 신호가 베어링에서 발생함의 증거입니다.
전체 6